Page 1 of 1
I can tig weld!
Posted: Fri Jul 23, 2021 6:14 pm
by sbaker345
And very few or you will or should care, but for the .01% who might be intrigued. You can get various tool steels, several you might recognize from the knife world as filler rod. A2, D2, S-7 tool steel, M2 to name a few. They're not cheap, a pound of rod would run me about 50-60 dollars, but turning a cheap Chinese tool into a sort of bimetal blade can have surprising results. I used a broken drill bit as filler rod on the edge of my chipping hammer simply relying on the mass of the rest of the hammer to quench it, and I was left with something that would chop gouges into my welding table, stainless steel plate or any other mild steel I swung it at without leaving the slightest perceptible hint of damage to the chipping hammer.
Just testing the waters here as to how many people would be interested in seeing things like cheap axes and such overlaid with actual tool steel and the difference in performance. as obviously the money could be put towards things like new knives or an actual way to sharpen my S110V manix as I don't have my wicked edge anymore.
Re: I can tig weld!
Posted: Fri Jul 23, 2021 11:11 pm
by Doc Dan
I don't know where you are located. Indeed and Monster had jobs listed for TIG Welders the other day.
Re: I can tig weld!
Posted: Sat Jul 24, 2021 12:28 pm
by TomAiello
That's interesting. Do you happen to have any photos of the hammer before and after?
Re: I can tig weld!
Posted: Sat Jul 24, 2021 3:07 pm
by jpm2
That broken drill bit you used as filler was probably M2. I used to demonstrate to my coworkers the durability of my m2 bladed knife by hacking the corner of the mild steel welding table, leaving deep marks in the table, and nothing on the blade. Them doing the same thing with their knife would roll and/or flatten their edge.
I repurposed a lot of scrap tool steels into other tools over the years. I've made knives, punches, gouges, chisels, ease outs, etc from things like drill bits, key cutters, parting tools, saw blades, etc.
My chipping hammer was home made, but don't recall which steel I made it from.
Re: I can tig weld!
Posted: Sat Jul 24, 2021 4:24 pm
by sbaker345
jpm2 wrote: ↑Sat Jul 24, 2021 3:07 pm
That broken drill bit you used as filler was probably M2. I used to demonstrate to my coworkers the durability of my m2 bladed knife by hacking the corner of the mild steel welding table, leaving deep marks in the table, and nothing on the blade. Them doing the same thing with their knife would roll and/or flatten their edge.
I repurposed a lot of scrap tool steels into other tools over the years. I've made knives, punches, gouges, chisels, ease outs, etc from things like drill bits, key cutters, parting tools, saw blades, etc.
My chipping hammer was home made, but don't recall which steel I made it from.
Yup m2 was my guess as well, although I'm still surprised a purpose built knife would hack into steel with the same lack of damage. I'd attributed it to geometry as I've never seen any knife survive steel on steel contact ENTIRELY unscathed. It's clear I'm not even the only person on this forum who's done this, yet, until a few months ago I had never considered the prospect a possibility. It's often funny the possibilities offered in the welding world far beyond simply "join this to that" which are not widely discussed. Perhaps it's just one of those things you learn around the time you've actually developed the skill to do it. It sounds like you've already done anything I could attempt to try, but I've just always had a bit of a fascination with.
The concept, simply seems like such a natural pairing with individuals like us who are willing to spend hundreds to have a quality reliable tool a step above what everyone else grudgingly uses. As for an entirely homemade chipping hammer that has been a bit of a dream of mine, to make my own quality chipping hammer sort of a way to blend one hobby with another career/hobby.
Re: I can tig weld!
Posted: Sat Jul 24, 2021 7:19 pm
by jpm2
sbaker345 wrote: ↑Sat Jul 24, 2021 4:24 pm
jpm2 wrote: ↑Sat Jul 24, 2021 3:07 pm
That broken drill bit you used as filler was probably M2. I used to demonstrate to my coworkers the durability of my m2 bladed knife by hacking the corner of the mild steel welding table, leaving deep marks in the table, and nothing on the blade. Them doing the same thing with their knife would roll and/or flatten their edge.
I repurposed a lot of scrap tool steels into other tools over the years. I've made knives, punches, gouges, chisels, ease outs, etc from things like drill bits, key cutters, parting tools, saw blades, etc.
My chipping hammer was home made, but don't recall which steel I made it from.
Yup m2 was my guess as well, although I'm still surprised a purpose built knife would hack into steel with the same lack of damage. I'd attributed it to geometry as I've never seen any knife survive steel on steel contact ENTIRELY unscathed. It's clear I'm not even the only person on this forum who's done this, yet, until a few months ago I had never considered the prospect a possibility. It's often funny the possibilities offered in the welding world far beyond simply "join this to that" which are not widely discussed. Perhaps it's just one of those things you learn around the time you've actually developed the skill to do it. It sounds like you've already done anything I could attempt to try, but I've just always had a bit of a fascination with.
The concept, simply seems like such a natural pairing with individuals like us who are willing to spend hundreds to have a quality reliable tool a step above what everyone else grudgingly uses. As for an entirely homemade chipping hammer that has been a bit of a dream of mine, to make my own quality chipping hammer sort of a way to blend one hobby with another career/hobby.
I've worked industrial maintenance all my life and over the years desired better tools. Sometimes that requires making your own.
All my benchmade m2 blades will hack mild steel with no apparent damage if the edge isn't too thin (less than 30 degrees inclusive). Some of my production m4 blades will do it, but not all.
I've made several fixed blades from scrap m3, m35, m42 and t42. Hacking a few times into the edge of a mild steel table is just one of many ways I've tested for edge stability. Mild steel is pretty soft btw.
All my welding was stick and wire, never got a chance to tig weld.
Re: I can tig weld!
Posted: Sun Jul 25, 2021 7:24 pm
by sbaker345
I guess I need to get a blade in m2 or possibly m4 then, it's simply inevitable.
Re: I can tig weld!
Posted: Sun Jul 25, 2021 7:46 pm
by Bloke
jpm2 wrote: ↑Sat Jul 24, 2021 7:19 pm
my welding
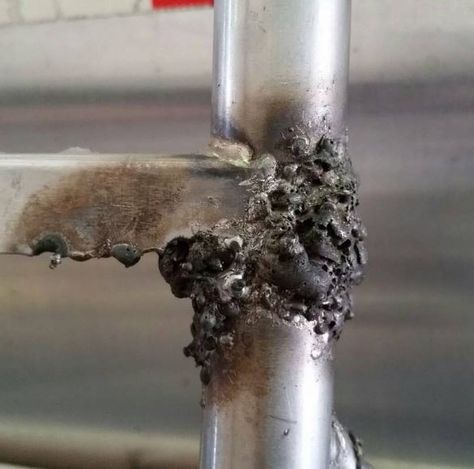
Re: I can tig weld!
Posted: Sun Jul 25, 2021 8:45 pm
by Sharp Guy
I can't tig weld!
My brother the gunsmith is very good at it. I leave those kinds of things to him :)
Re: I can tig weld!
Posted: Mon Jul 26, 2021 7:37 am
by VashHash
Tig welding is pretty cool. I learned to braze weld with a torch when I was younger. Did stick welding, mig welding, and Fluxcore. Never learned tig but it has a lot of benefits to other welding styles. I remember training in school and watching a guy tig weld a bike frame back together.
Unfortunately bloke I've seen welds like that. Our company has to pass mag testing/dye penetrant and hydro testing. The guys that weld like that don't last very long.
Re: I can tig weld!
Posted: Mon Jul 26, 2021 10:28 am
by RustyIron
sbaker345 wrote: ↑Sat Jul 24, 2021 4:24 pm
Yup m2 was my guess as well, although I'm still surprised a purpose built knife would hack into steel with the same lack of damage. I'd attributed it to geometry as I've never seen any knife survive steel on steel contact ENTIRELY unscathed.
I've got a couple homemade Burr Knives. They're handheld tools used mostly for chamfering the corner off a rotating part that I just finished boring in the lathe. While you can buy tools for this purpose, I've never seen one I liked. A homemade burr knife will be made out of some kind of broken or unsalvageable cutting tool. Grind it to shape, put a handle on it, et voilà! The one in the picture is ground to three corners, so it's about 120 degrees per cutting edge. "Shaving sharp" is not the goal. A bit of pressure is used, and as you move the burr knife around, you'll feel when you get the right angle. It's used on steel, bronze, aluminum, plastic... it doesn't matter. Usually no damage occurs tot he tool, but eventually the surfaces wear and need to be touched up.
.
Re: I can tig weld!
Posted: Mon Jul 26, 2021 10:09 pm
by jpm2
Bloke wrote: ↑Sun Jul 25, 2021 7:46 pm
jpm2 wrote: ↑Sat Jul 24, 2021 7:19 pm
my welding
haha, that's pretty bad. Kinda resembles a dirt dobber nest.
Re: I can tig weld!
Posted: Sun Aug 01, 2021 7:49 pm
by sbaker345
Bloke wrote: ↑Sun Jul 25, 2021 7:46 pm
jpm2 wrote: ↑Sat Jul 24, 2021 7:19 pm
my welding

how, I honestly want to know how, Is that slag from trying to stick weld what looks like pretty thin wall, and possibly either coated or stainless tubing. I'm impressed in a horrified kind of way.
Re: I can tig weld!
Posted: Mon Aug 02, 2021 5:40 am
by Bloke
RustyIron wrote: ↑Mon Jul 26, 2021 10:28 am
I've got a couple homemade Burr Knives. ..
Hey Rusty, I learned early in my time as a young apprentice the value of a decent debarring tool.
I still have a three corner “scrapper” I made around my 2nd year. It’s a hollow ground (though many times sharpened now, on a flat stone) three corner file. I still use it today on my little lathe at Mum and Dad’s place (otherwise I’d post a pic).
I must have made it around 1977 and marvel at my skill and eyesight at the time. Ah, hahaha! And, I still haven’t found anything that holds a candle to it.
Re: I can tig weld!
Posted: Thu Aug 05, 2021 6:38 pm
by me2
sbaker345 wrote: ↑Sun Aug 01, 2021 7:49 pm
Bloke wrote: ↑Sun Jul 25, 2021 7:46 pm
jpm2 wrote: ↑Sat Jul 24, 2021 7:19 pm
my welding

how, I honestly want to know how, Is that slag from trying to stick weld what looks like pretty thin wall, and possibly either coated or stainless tubing. I'm impressed in a horrified kind of way.
I’ve been a welding inspector for 18 years. I’ve seen worse, but not much.